Tag: hot dip galvanizing firms
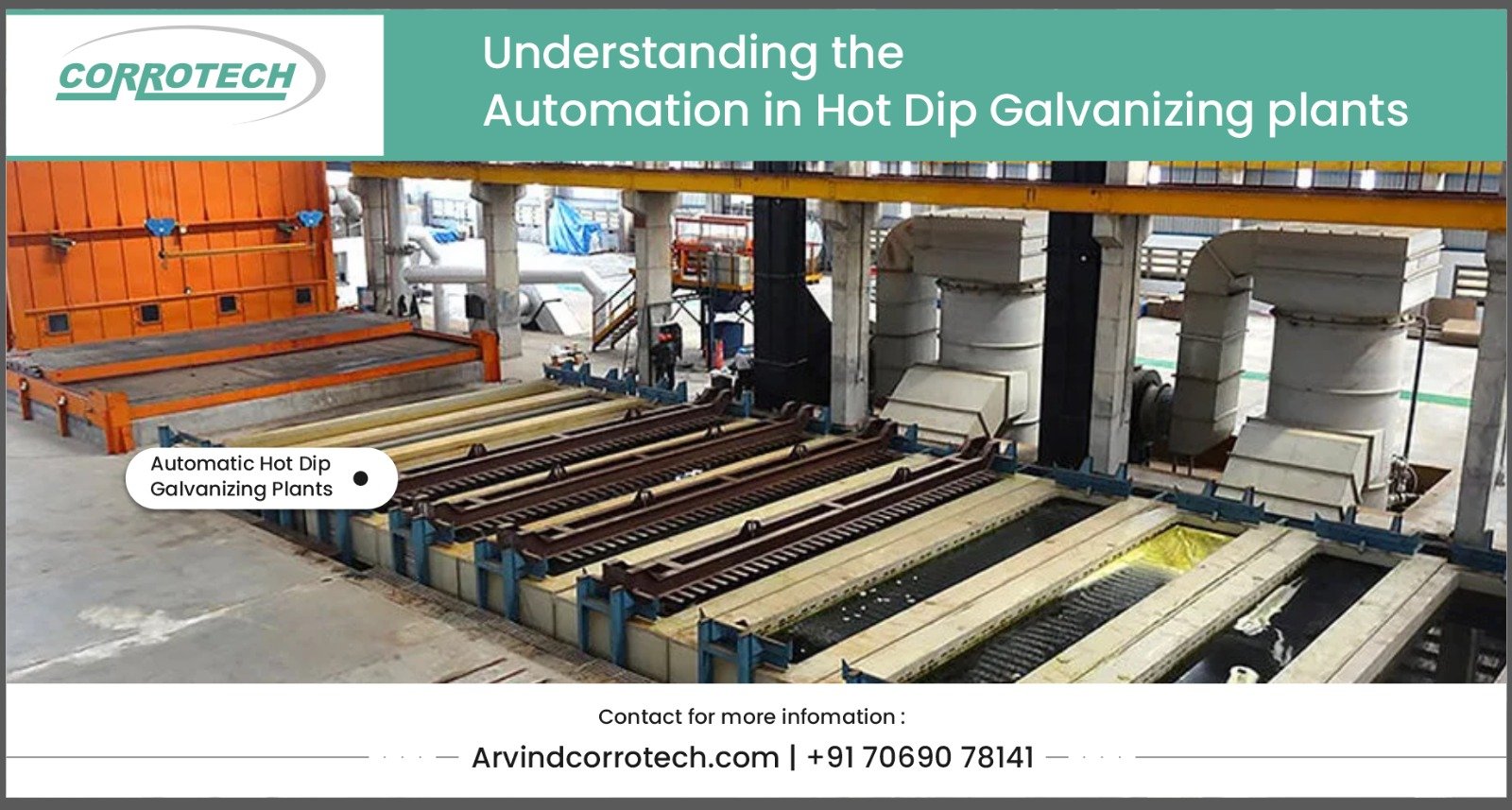
Businesses aiming at improving the efficacy and quality of their galvanizing procedures should think about investing in automatic hot dip galvanizing plants. The latest technology in automatic plants enables the automation of many galvanizing procedures, resulting in greater output and uniform outcomes.
Understanding the components of these plants is very important for making decisions regarding implementation and operation. In this blog, we will understand the essential components of Automatic galvanizing plants, and also the function and benefit of each component.
-
Pre-Treatment section
The first stage in the galvanizing process is the pre-treatment section. This stage is important for preparing metal or in simple terms steel products for coating. The things which are included in this section are:
- Degreasing Tanks
These tanks help in removing the excess oil, grease, and other oily substances which are present on the steel surface. A completely clean surface is very essential before the zinc coating.
- Pickling Tanks
These tanks are filled with acid solutions and help in removing rust, scale or any such oxide from the steel. The use of this tank provides a proper smooth and clean surface for galvanizing.
- Rinsing Tanks
After pickling the steel with acid, the steel is again rinsed in the tank to remove the leftover acid from the surface.
The benefits of the Pre-Treatment section are:
- Provides clean and smooth steel surfaces.
- Will help in giving the proper zinc coating.
- Will improve the quality of the final product.
- Fluxing section
In this section, the clean steel is dipped into a flux solution, which is simply, ammonium chloride. This step is important as it prevents oxidation. The different components of this section are:
- Flux tanks
These tanks have flux solutions, which help in promoting the bond of zinc and steel.
- Drying ovens
Steel parts after fluxing are dried properly in this oven to remove any sort of residual moisture and to ensure uniform zinc coating.
The benefits of the fluxing section are:
- It helps prevent oxidation.
- It helps in providing a strong bond between iron and zinc.
- It helps in improving the quality and durability of the galvanized coating.
- Galvanizing Kettle
This is the most important component of the galvanization process. It has molten zinc which has a temperature around 450°C.
The different components of this include:
- Kettle
The kettle which is used is made up of steel and has ceramic linings, it is used to hold molten zinc for the dipping process.
- Heating System
This system helps in ensuring that the zinc is at the appropriate temperature which is very important for effective galvanizing.
- Dipping mechanism
This mechanism is used for raising the steel parts into and out of the molten zinc, to provide even coating.
The benefits of Galvanizing Kettles are:
- It helps in providing uniform zinc coating.
- It increases corrosion resistance.
- It ensures the durability of the steel products.
- Cooling and Quenching section
After coating the steel parts with zinc, the parts need to be cooled and solidified. This section of the galvanizing process includes:
- Cooling tanks
In this tank, the galvanized steel is cooled using either water or air to solidify the zinc coating properly.
- Quenching tanks
This tank is mostly filled with passivation solution, to enhance the appearance and corrosion resistance property of the zinc coating.
The benefits of the Cooling and Quenching section include:
- The rapid cooling helps in solidifying the zinc coating.
- The passivation which is provided helps in improving corrosion resistance and appearance.
- This section provides durability to the galvanized products.
- Post-treatment section
This section involves additional processes, to improve the quality and finish of the galvanized products. The processes involved are:
- Inspection and finishing
The automated galvanizing plants, in this process, inspect the galvanized products to ensure that there are no defects or uneven coating. Finishing the product includes removing the excess zinc and also adding protective coatings.
The benefits of the Post-treatment section are:
- This section ensures that there is no defect in the product.
- It helps in improving the appearance and durability of the products.
- It prepares the product for safe transportation.
- Control systems
There are advanced control systems which are integrated into the automatic galvanizing plants, to ensure precision and efficiency.
- Programmable logic controllers
These controllers control the entire process from pre-treatment to post-treatment ensuring that each stage is operating correctly.
- Monitoring systems
These systems provide real-time data based on process parameters, which allows adjustments to maintain the optimal temperature.
- Safety systems
They help in protecting the workers and different instruments from any potential hazard.
Benefits of control systems
- It helps in improving the operational efficiency.
- It provides consistent quality and adherence to standards.
- Provides safety and reduces the risk of accidents.
Conclusion
Investing in a proper Automatic Galvanizing plant or a Turnkey hot dip galvanizing plant can provide many advantages like increased efficiency, consistent results, and enhanced safety. Understanding all the key components helps the businesses to make proper decisions about the implementation and operation.
We at Arvind Corrotech, are leading galvanizing plant manufacturers and provide all the solutions according to your needs. By using advanced technology and automation, hot dip galvanizing plants can improve your production capabilities and provide you with high-quality galvanized products.

There are several hot dip galvanizing plant manufacturer Ahmedabad India, provide the galvanizing plant. With the numerous years of experience in the field, Arvind Corrotech is the leading turnkey hot dip galvanizing plant supplier.
The galvanizing plant is with the aid of using par one of the maximum ecological strategies of galvanizing the metal with the zinc. The process is done to make the meta corrosion-free and make it durable for a long time. The manufacturerus all in one package with the several units and provide the hot dip galvanizing. With the packages in which metal are uncovered to severe atmospheric conditions. The hot dip galvanizing firms make these products to galvanized with the zinc.
- Metal Pipes
- Electrical Poles
- Road Side Barriers
- Steel Towers Used For Electrical Transmission
- Cable Trays
- Steel Towers Used For Mobile Towers
- Fasteners
- Hardware Industrial Items
This plant is a genuine production system throughout some steps of the galvanizing plant. Other pre and post processes should be followed by the plant exporter. A spectrum of the pickling or process tanks used for removing the extra dust, and they consist of the acid or other chemicals.
The tanks are resistant to a wide range of chemicals, also they have great mechanical properties. The tanks are supplied from the exporter Ahmedabad India available in the PPH pp and pp-FRP as well. All the storage tanks should be easy to operate, and the tanks should be manufactured in vinyl ester fitted with the granite.
All the tanks are available in various shapes and sizes that suit every batch of the pickling material. The things such as sheet metal components, wire, pipe mills, and cr mills can be pre-processed before galvanizing plant.
Components To Be Used For Galvanizing Plant:
- Pre-Treatment Tanks
- Pulse Fired High-Velocity Furnace
- Zinc Kettle
- Acid Fume Extraction System
- Flux Heating System
- Acid Storage Tanks
- Effluent Treatment Plant
The zinc galvanizing process can be followed step by step by using the component listed above.
The Hot Dip Galvanizing firms make the galvanizing plants that can help you in galvanizing with the:
- Rapid Application
- Reliability
- Proper Mechanical Resistance
- Lower Production cost
- Easy Maintenance & Testing Of Galvanizing Quality
- Ultimate Protection
At Last,
The material can be galvanized by using the perfect hot dip galvanizing plant if it is employing top quality that credits all the components of the plant. Besides, to check the associated with the galvanizing plant, you should consider the top manufacturer, supplier, or exporter.

The enormous and remarkable economic challenges have introduced the need to utilize limited resources in an efficient and effective manner. The impact of currency devaluation along with globalization and environmental concerts are changing the overall governance to a high extent.
Why Make Generous Usage of Hot Dip Galvanizing Plant?
High technological advances have enabled some exclusive ways of deploying services in a cost-effective and timely manner. The generous usage of hot dip galvanizing plant is a great example. Yes, along with having a firm grip on preventing corrosion; it has proved to be an environmental friendly and cost effective solution.
Galvanizing plants have made it easy for governments to take best decisions for building and expanding their infrastructures to remain competitive in:
- Tourism
- Transportation
- Economy
Turnkey Hot Dip Galvanizing Plant Helping to Prevent Corrosion
Governments continue to focus on expanding militaries and managing political systems to expand national infrastructures. To ensure that these facilities operate at optimal level, effort is being geared to preserve them from corrosion,turnkey hot dip galvanizing plant has proved to be of great help.
Such plants will prevent controlling corrosions to a high extent, thus ensuring maximal services to citizens. Top hot dip galvanizing firms are adopting the most suitable technological solution to the hazards will truly extent the usefulness of such facilities. Also, it will benefit both the nation.
Painting and Plating Remains No More Effective Today
Generally, painting and plating are common methods used to prevent the ill effects of corrosion. Though partly effective, it will be a good idea to go with a top manufacturer of galvanizing plant. It has proved to be a reliable, cheap and durable method of preventing rusting hence causing less harm to the environment.
In case you are unable to halt to the best decision, better have a detailed discussion with a reliable supplier in Ahmedabad. It will give you an insight to the merits along with methods of maintaining these plants.
Remarkable Benefits of Hot Dip Galvanizing Plants
Want to know what attracts industries towards hot dip galvanizing plants? Below are some remarkable benefits assured by top exporters in India:
- Low cost and less labour intensive
- Highly durable with less maintenance
- High life expectancy of minimum forty years
- Process is simple, controllable and straightforward
With a wide variety of options available in the market, it will become easy to select the most suitable galvanizing plant for your needs.