Category: Uncategorized
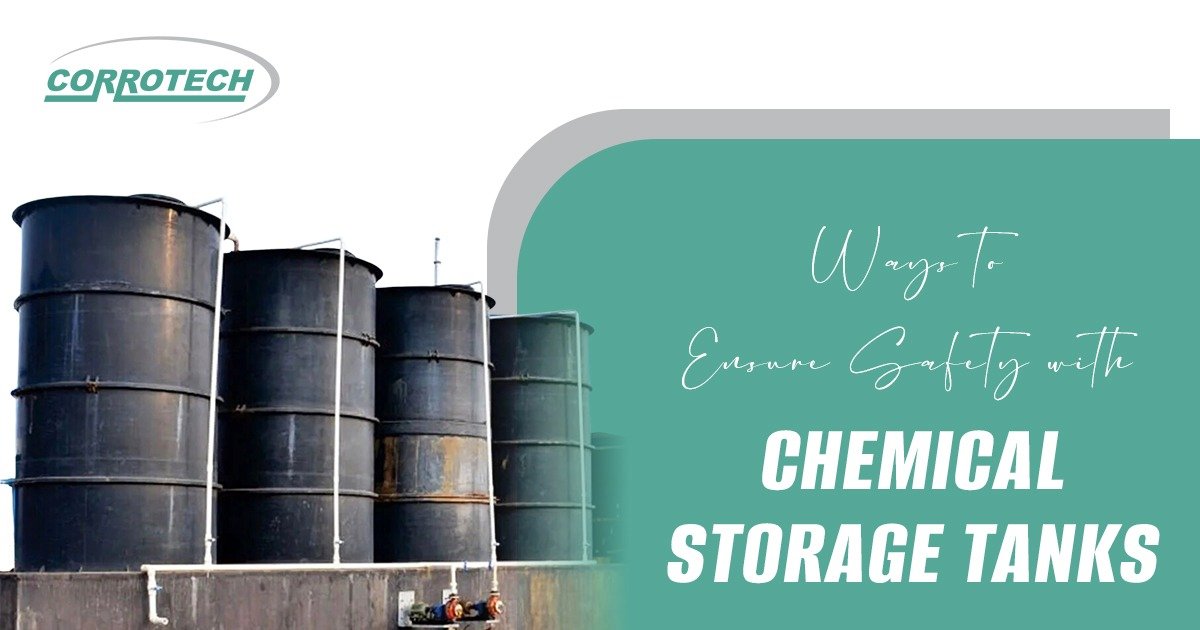
Safe and efficient management of chemicals is crucial when it comes to the modern industrial landscape. Doesn’t matter whether it is a big industry or small, or whether you are running an industry related to food & beverage, pharmaceuticals, manufacturing, or agriculture, chemical storage tanks play an important role in every operation. So, in this blog we will discuss why chemical storage tanks are beneficial for any industry.
-
Safety First
One of the major benefits of keeping a chemical storage tank is it has the ability to reduce the risk of leaks and spills, which can be dangerous. Modern chemical storage tanks are designed keeping all the safety features in mind such as leak detection system, double-walled construction, and pressure relief valves. Chemical tanks have features that help contain harsh materials along with minimum environmental contamination which not only protects the employees but also the surrounding community. In addition to this, proper storage of chemicals helps in complying local and national safety guidelines, which makes sure that your facility meets the required standards. Therefore, it is important to stay committed to safety as it fosters a sense of responsibility and enhances the company’s reputation.
-
Flexibility in Storage Solutions
Chemical storage tanks are definitely an excellent invention as it makes chemical storage a flexible thing. This is because chemical storage tanks come in multiple sizes and configurations which allows the industries to select the right solution as per their preference. You can go for small tanks for temporary projects to larger ones for long-term storage. There are limitless options in chemical storage tanks as these tanks can be customized to accommodate different types of chemicals. This also helps industries in adapting storage solutions as per their needs because flexibility is crucial in this fast-paced business environment.
-
Better Control of Chemical Properties
There are certain chemicals in the market that need specific storage space and proper maintenance. In this situation, you can opt for chemical tanks as these are designed to provide controlled environments by protecting sensitive materials which include contamination, fluctuation, and moisture. Optimal storage conditions ensure businesses that their chemicals perform as intended which will enhance the quality control and reduce the likelihood of product failures. Understanding that your business has better control of chemical properties is crucial in businesses like food production and pharmaceuticals, where quality is the king.
-
Improved Inventory Management
To make your inventory management better, go for chemical storage tanks as it provides a centralized location for chemical products. This centralization approach makes other tasks easier like track usage, stock levels, and re-ordering schedules. Allow your business to gain real-time insights through advanced monitoring systems as it ensures that they always have the right amount of chemical on hand, without running out or overstocking. This efficiency eases the streamlined operations and allows your team to focus more on strategic tasks rather than managing chaotic inventory levels.
-
Enhanced Operational Efficiency
Businesses run for longer because of their operational efficiencies and the ability to produce within deadlines. This efficiency can be enhanced by the use of chemical storage tanks as it contributes greatly to the storage solution and handling of the chemicals. With chemical storage tanks, employees can access the materials quickly which they need without the delays associated with smaller containers or storage locations. In addition to this, there are multiple tanks that are associated with automated systems which steamline the transfer of chemicals. Go with a high-tech chemical storage tank as it not just reduces the extra work of manual labor, but it also minimizes the time spent on processing and managing the material.
For businesses, chemical storage thanks are an invaluable asset as it handles hazardous chemicals easily. From reducing costs to improving inventory management to enhancing safety, chemical storage tanks ensure compliance with environmental regulations along with holding multiple benefits. Remember to invest in the right chemical storage solutions as this will not only protect your business or the workplace, but it will also support sustainable practices and operations. The business industry is growing, and in the coming future, the use and importance of chemical storage tanks and management will only grow. So make your operations successful and grow in the market, invest in Arvind Corrotech‘s chemical storage tanks, and make a calculated investment now.
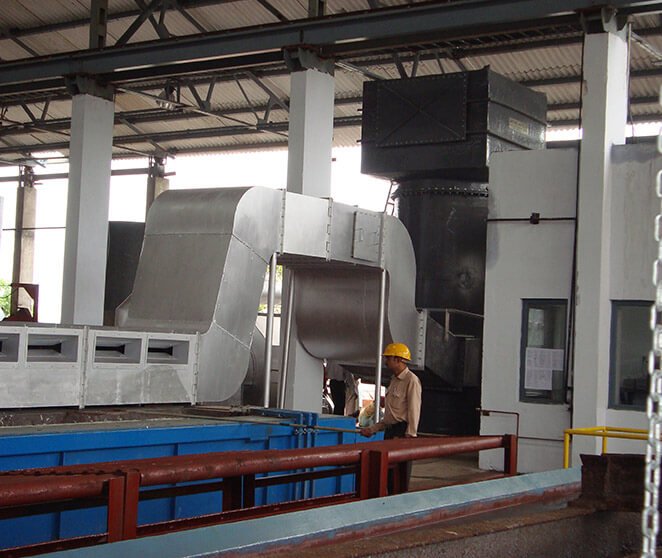
In this manufacturing industry-centric blog, we are going to highlight an important system, the fume extraction system, its importance for galvanizing plants, its salient features, etc.
Before we take a deep dive into the subject, it’s logical to learn about the exhaust extraction system.

Learning about the exhaust extraction system
A wide range of industrial processes creates and generates harmful fumes during different processes. The harmful fumes are present in a variety of forms, sanding, spraying, powder filling, grinding, welding, and chemical applications among others. The fumes, if not captured and extracted, lead to various repercussions, including health issues for the workforce and degradation of plant machinery.
A portable fume extractor is a sophisticated system designed and engineered to pull fumes, dust, hazardous pollutants, and a host of other harmful particles into a contained filtration system. The scientifically designed system’s main objective is to remove harmful air pollutants.
Why is fume extraction system a must for hot-dip galvanization?
The hot dip galvanizing process has emerged as one of the most effective systems for galvanization. During the process of galvanization, white fumes get generated when metal-made items/ steel is dipped in the molten lava of zinc. The fumes that get generated are extremely hazardous due to the presence of chlorine and suspended ash particles. Fume is harmful to health and the workforce. Furthermore, fumes deteriorate the overhead cranes and the shed life. Therefore, it makes sense to establish a system for fume abatement and discharge.
Components of a standard exhaust extraction system
A standard fume extraction system comprises a fume extraction hood (lip extraction duct, fixed fume enclosure, crane mounted enclosure), dust collecting cyclone (dust collector) that is connected to the wet scrubber, and a bag filter). The high efficiency system is designed for air filtration, clean air, air quality. It comprises extraction units for source capture.
Working mechanism
Let’s now shift our focus towards the working mechanism of the important system for capturing fumes. Many of you are curious to learn its mechanism. The anti-pollution system has fume extraction. The sturdy hood is attached to dust collecting cyclones. Harmful heavy ash particles that are present inside the zinc fume settle down at the bottom of the cyclone. This cyclone is connected with the zinc fume wet scrubbers. Cyclone is designed to function as a cleaner and filter. Here fumes are cleaned and filtered and eventually released into the environment with the help of a stack.
Benefits and advantages of the exhaust extraction system
The high-end exhaust extraction system is providing numerous benefits to manufacturing companies, these include:
- Increased productivity
- Eliminates white fumes
- Improved health of workers
- Creates a safe and healthy environment
This scientifically designed fume extraction system is also known as the white fume extraction system as during the galvanization process white fumes get extracted. Furthermore, mobile fume extractors are also available in the market that ensures healthy working environments and breathing zone
Industries where a fume extraction system is widely used
There are numerous industries wherein the exhaust removal systems are used to control pollution in the manufacturing setup, including:
- Galvanization
- Textile
- Chemical
- Pharmaceuticals
- Foundries
- Welding
- Laser cutting
- Cement
- Steel
An exhaust extraction system is beneficial for a number of jobs
With an efficient anti-pollution system, a wide range of jobs are perfumed, including:
- Cutting
- Grinding
- Spraying
- Sanding
- Chemical Applications
- Smelting
- Brazing
- Molding
- Welding
Conclusion
The exhaust extraction system is an amazing product that helps industries in playing their bit toward a healthy environment. Sustainable development is the need of the hour and it’s a brilliant move to install a fume extraction system.

In this blog, we are going to focus on zinc fume enclosures. It is also called a white fume capture and abatement system.
White fumes that are discharged by the immersion of steel in the kettle filled with molten zinc during the process of galvanization are hazardous in nature if inhaled. Also, it causes environmental pollution, breaking the pollution control rules, as it is discharged in excess. Therefore, it becomes inevitable to equip every hot-dip galvanizing plant with a proper white fume capture and abatement system.
In the ensuing section, we are going to cover a few important subjects related to the critical subject.
Premium quality high-performance white fume enclosure system provides almost 100 percent efficiency for fume abatement.

Efficient fume extraction
With quality-driven designed enclosures, the fume escape is limited to its absolute minimum. The enclosure is connected with a dust collecting cyclone which is further connected with a wet scrubber or a bag filter where fumes are cleaned for efficient filtering before it exits into the atmosphere. This is a classic example of efficient fume extraction.
Major types of Zinc Fume Enclosures
Continued technological advancements are helping zinc fume enclosures manufacturers to come out with a modern efficient fume extraction system. Primarily it is of two types:
- Fixed fume enclosure over the furnace
- Crane mounted enclosure
How to select the perfect fit for your corrosion technology unit?
Which design will fit your requirement? It primarily depends on the type of equipment layout.
Leading zinc fume enclosures manufacturers in Ahmedabad, India design the enclosure system with utmost excellence, keeping the safety factor in mind. Both the enclosure systems have sliding doors and side windows for quick and easy ash skimming, ensuring workers’ safety against falls and splashes.
The fume enclosure system allows you to stay in compliance with the requirements of the pollution control board, industrial safety, and health regulations.
Salient features of an efficient fume extraction system
- Pneumatically and hoist operated doors
- Splash-proof
- Easy accessibility for skimming zinc ash
- Viewing windows having toughened glass fixed over a steel frame
- Easy to remove the kettle
- The extraction duct is placed on the roof and connected with the bag filter, cyclone, and scrubber
- Easy to operate
- Low maintenance cost
- Durable
Benefits
Let’s now shift towards another vital subject related to this industry-centric blog, the benefits. How does an efficient fume extraction benefit the industry? Here is the list of benefits identified with a premium quality Zinc Fume Enclosures:
- Increased shed life by eliminating fumes
- Improved visibility on the shop floor
- Eliminates safety and health risks due to the hazardous fumes
- Eliminates accidents of serious nature in event of zinc splash
Cost-saving
The quality-driven zinc fume enclosures lower zinc and fuel consumption. With lower zinc and fuel consumption, companies save money. Cost-saving is directly proportional to revenue. Therefore, it is imperative to buy the product from leading manufacturers. Never settle for less. Quality doesn’t come cheap. It’s worth investing in a quality-driven plant, businesses are bound to reap fruits.
Conclusion
Keeping in view the significance of an efficient fume extraction system, the majority of companies are integrating it into their manufacturing process. If you are looking for an efficient fume extraction system, don’t go further. End your search with Arvind Corrotech.

Conservation of the environment assumes significance in this era of rapid industrialization. Ever-increasing population further pushes the need for industrialization, leading to pollution. ETP plant helps in the reduction of pollution and strikes a balance between industrialization and sustainable development.
Without a safe and healthy environment, sustainable development can’t be imagined, therefore, it makes sense to promote sustainable development. It is a great way to conserve and enhance our resources, by altering the manners in which industries and factories work and discharge waste material. ETP treatment plant is an ideal step towards the conservation of the environment and sustainable development.
In this blog, we are going to highlight about ETP plant, waste water treatment and how the sophisticated machine helps in environment conservation.
Before we move forward, let’s understand ETP in simple language. The definition will help you to connect with the blog in a better way and expand your knowledge.

Learning about the brilliant ETP Plant
ETP stands for Effluent Treatment Plant. It is a mechanized system designed and fabricated to treat industrial effluents.
Waste treated by the plant
As an owner of the manufacturing industry or someone holding a key position in a factory, it’s your responsibility to understand the machine you are about to procure. Types of waste treated by the machine is an important query that often crosses the mind of buyers. Feel free to ask the manufacturer.
A typical ETP treatment plant is designed for primary treatment of multiple types of waste discharges of manufacturing units, including:
- Organic matter
- Inorganic matter
- Heavy metals
- Oil & grease
- Removal of suspended particles
- Chemicals
- Domestic waste
- Toxic
- Non-toxic
- Suspended solids
Furthermore, the scientifically designed wastewater treatment plants are apt to treat many other types of industrial discharges.
Types of the waste treatment plant
Apart from standard effluent plants, waste treatment plant manufacturers in Ahmedabad India also manufacture specific kinds of waste treatment plants, including:
- Chemical treatment
- Biological treatment
- A combination of chemical and biological treatment
- Thermal treatment
The process
The plant is designed to work through an exclusive process. The process comprises the Physico-chemical treatment of waste. It is followed by polishing treatments, including sand filtration, activated charcoal treatment (adsorption), ozonization (chemical oxidation), ultra-filtration (UF), and reverse osmosis (RO) and evaporation. Evaporation depends on the requirement.
Industries drawing benefits
Keeping in light the advantages and benefits of the ETP plant, the machine is used in numerous industries and factories, including:
- Textile
- Pharmaceuticals
- Cement
- Chemicals
- Paper
- Paint
- Steel
Benefits and advantages of ETP
Waste water treatment processes are rapidly assuming significance, riding on its role in aiming to protect the health of the ecosystem and conservation of the environment. Treated wastewater is suitable for many purposes, including gardening and farming. Now it’s time to highlight the benefits of the environment-friendly water treatment plants. Why shouldn’t industries undermine the benefits of excellent inventions?
- Here are the benefits to further validate its importance for the industries:
- Saves and conserves the environment
- Prevents waterborne diseases
- Safeguards public health
- Minimizes damage to industrial products and machinery
- Processed water is reused
Can the ETP treatment plant treat acts as a sewage treatment plant?
Many of you might be thinking about this question. According to industry experts, the effluent treatment plant or etp machine is ideal for the treatment of not only industrial waste but also suitable for the treatment of domestic sewage waste.
Conclusion
It’s our joint responsibility to conserve the environment. ETP treatment plant is a brilliant step forward. Start installing industrial waste water plants now . If you are looking for a premium quality ETP treatment plant manufacturer, then end your search with Arvind Corrotech.
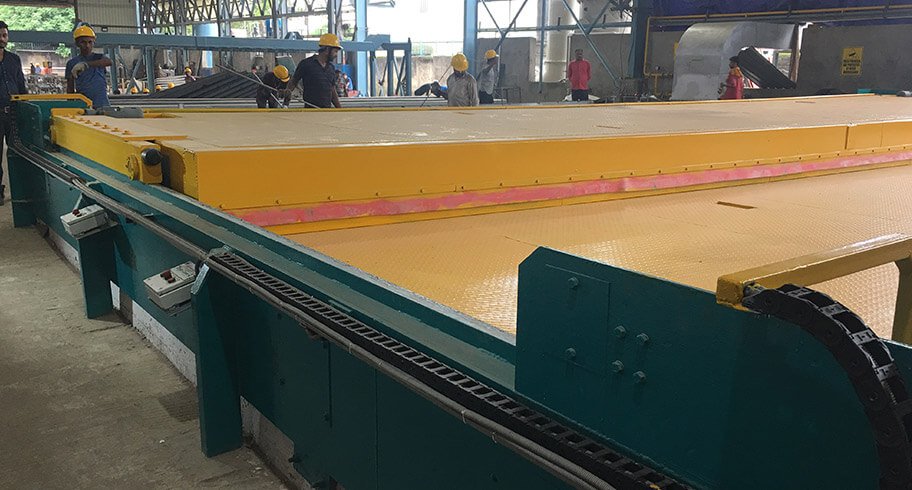
In this industry-centric blog, our focus will be hot air circulation dryer, its features, and how it impacts the galvanizing industry.
Before we take a deep dive into the crucial manufacturing industry-related subject, it makes sense to learn about the product in plain language. It will help the readers in connecting with the content better and expand their knowledge about hot air dryer.

Learning about the hot air dryer
The quality-driven and precision engineered machine is integrated with the galvanizing furnace. It is designed and manufactured to pre-heat the structural steel by re-circulating the exhaust flue gases that generate from the furnace. The hot air is utilized for complete drying and preheating of the steel/ metal to be hot dipped in the molten zinc. It facilitates a faster reaction. Consequently, this leads to reduced fuel consumption. Additionally, controls the loss of zinc due to spurting. Sounds amazing, that’s how the machine impacts the hot dip galvanization mechanism.
Salient features of a quality-driven hot air circulation dryer
From the basics, let’s now shift toward the salient features of the product. Why? As an owner of a company that is using the galvanizing plant for the galvanization of products, it’s vital to install and commission-only a quality-driven product. The reason is – that only a quality-driven product with drying chamber has the competency to meet your business goals. The ensuing content talks about salient features of the product:
- Energy efficiency
- Sturdy design
- Proper temperature rated components,
- Proper sizing of air recirculation (to get a reasonable air velocity and number of air changes per minute) and burner components,
- Powerful exhaust system and air flow
- Oven workmanship
- Detailed operation and maintenance manual
- Easy to install and commission
- Easy to maintain and clean
- Optimized and uniform heat distribution
- Durable
Important design qualities of the machine
While buying the machine, don’t forget to raise important design features to the manufacturer and supplier, including:
- Heat recovery system that eliminates the requirement of auxiliary burners.
- PLC based automatic temperature control system
- Uniformity of temperature
- Uniformity of airflow
Benefits of hot air circulation dryer for industries
Now it’s time to bring focus on another important issue, the benefits of hot air circulation dryer. Here are the advantages of the product for our readers. It will further expand the knowledge of readers and at the same time advocate the use of the machine in the galvanizing setup.
- Lower zinc consumption
- Minimizes fuel consumption
- Competent to eliminate zinc splash
- High product quality
- A clean environment in the workplace
- Creates a safe working environment for workers
- Energy conservation
The hot air dryer machine operates within an open cycle. The ambient air is fetched through a filter, allowed to heat, and then passed through the resin granulate in the drying hopper. Afterward, the hot air vented to the factory floor.
For detailed information, you can get in touch with Arvind Corrotech, a leading hot air dryer manufacturer in Ahmedabad.
Control of drying temperature
How to control the drying temperature? This is an important feature of the quality-driven hot air dryer. A quality-driven machine is competent to control drying temperature and airflow by the blower unit.Heat transfer
How does the hot air dryer transfer heat? The machine is designed to transfer heat through the convection mode.
Last but not the least, the current relative humidity of the ambient air is a key factor as it impacts the outcome of the machine.
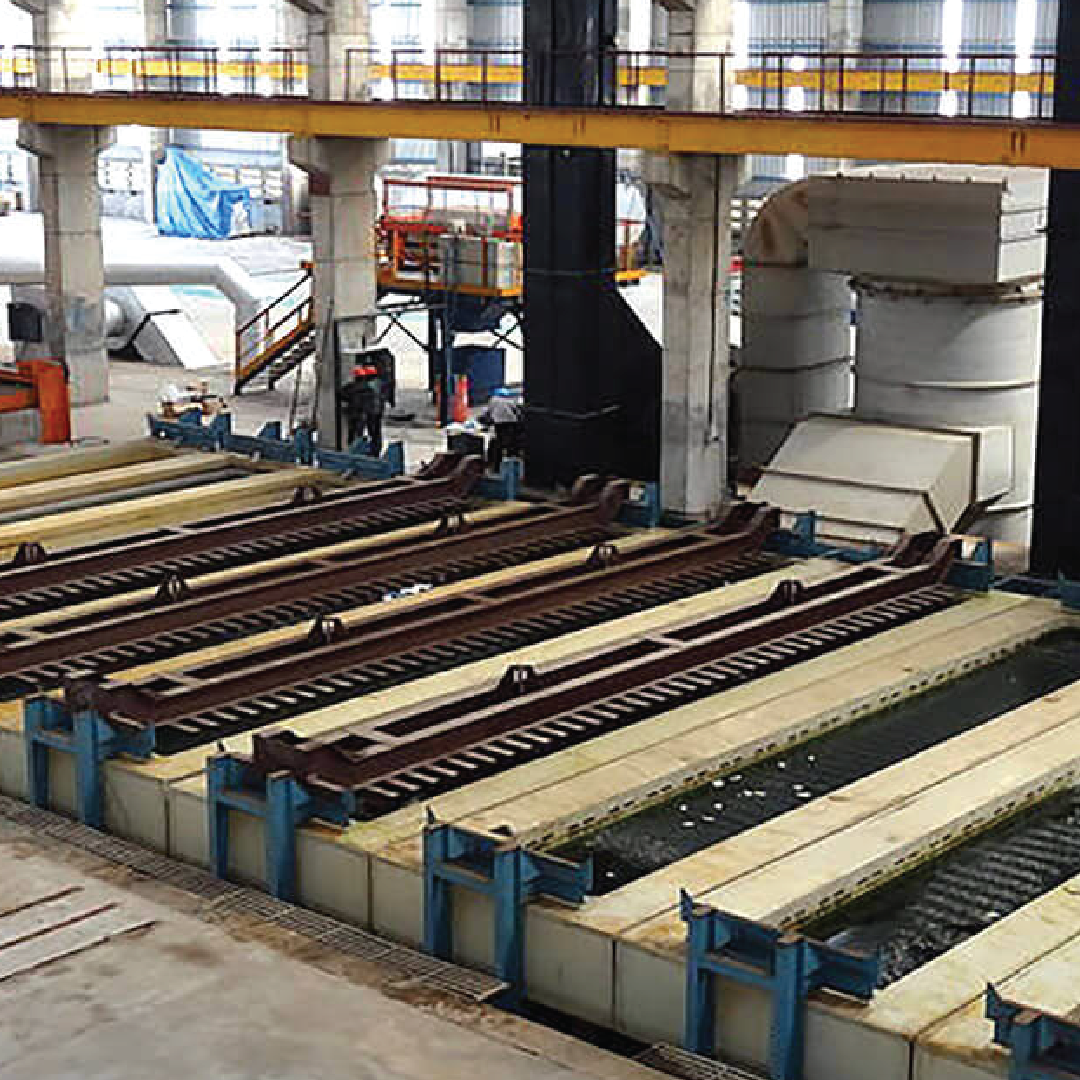
In this manufacturing industry-centric blog, we are going to focus on an important subject: costing of galvanization plants and their technology. Many of you have this perception that hot dip galvanizing technology is expensive, it’s beyond the reach of the normal manufacturer. In the ensuing section, we will highlight many relevant issues.
At the outset, it makes sense to understand the hot dip galvanization as it will help you to relate to the subject better.

Learning about the Hot dip galvanization
Simply put, the hot dip galvanizing process is a unique scientific process wherein steel/ metal objects are immersed into molten lava of zinc. As a result, a scientific reaction takes place. The metallurgical reaction forms a coating over the object. Subsequently, the metal develops numerous properties and features, primarily resistant to corrosion.
The formation process
This is a sophisticated process that helps in the process of forming an iron zinc alloy between the iron matrix and the outermost pure zinc layer. As a result of the scientific process, the iron-zinc alloy layer is formed on the surface of the object.
Process of Coating
From the basics, let’s now move to the process of hot dip galvanizing technology. The below information will give you significant information about the process:
Workpiece → Degreasing → Water Washing → Pickling → Water Washing → Dipping Helping Solvent → Drying and Preheating → Hot-dip Galvanizing → Finishing → Cooling → Passivation → Rinsing → Drying → Inspection
Hot dip technology
Let’s now move towards the hot dip galvanizing technology. The sophisticated process comprises scientifically proven steps and stages combined with the latest technology. It comprises:
- Degreasing
- Pickling
- Immersion flux
- Drying and preheating
- Hot dip galvanizing
- Finishing
- Passivation
- Cooling
- Inspection
Hot dip galvanization costly?
From the fundamentals, let’s now shift our focus to the most crucial subject of the blog.
Is it costly? Is it beyond the reach of small and medium manufacturers? Many of you might have struggled with similar questions. In the following section, we are going to solve the complex subject.
This needs to be understood with an example. According to research the overall cost of protecting a steel object or frame throughout its life depends on numerous factors, including the cost of paints, coatings, frequency of painting, any other relevant treatment, the life of the object, etc.
It has been observed that over a period of 20-25 years, the cost of paint will almost be around 70% more than the cost of galvanizing. While hot-dip galvanization technology offers a durable and maintenance-free life of the product.
Considering the lifetime costs, the latest system of galvanization proves to be considerably cheaper in comparison to other systems of galvanization. In other words, it costs less, lasts longer.
When you buy a galvanized material like a galvanized gate, you will have to pay more than an ordinary metal gate. However, the corrosion-resistant property and features of galvanization make it highly durable. It is worth investing in galvanization.
For further information about the cost of galvanizing plants and its technology, you can connect a few leading hot dip galvanizing plant manufacturers. In this era of technology, finding an established galvanization plant is just a click away.
Browse search engines with keywords like hot dip galvanization. The search engine result page will come up with web pages. Click on a few pages. Browse the website properly.